Revolutionize fluid hauling with predictive dispatch
Integrate SCADA sensors for automated job dispatch, track driver progress in real-time, and ensure accuracy with skid-measured volumes. IronSight automates and verifies each step, from dispatch to auto-approval, streamlining your fluid hauling operations with precision and reliability.
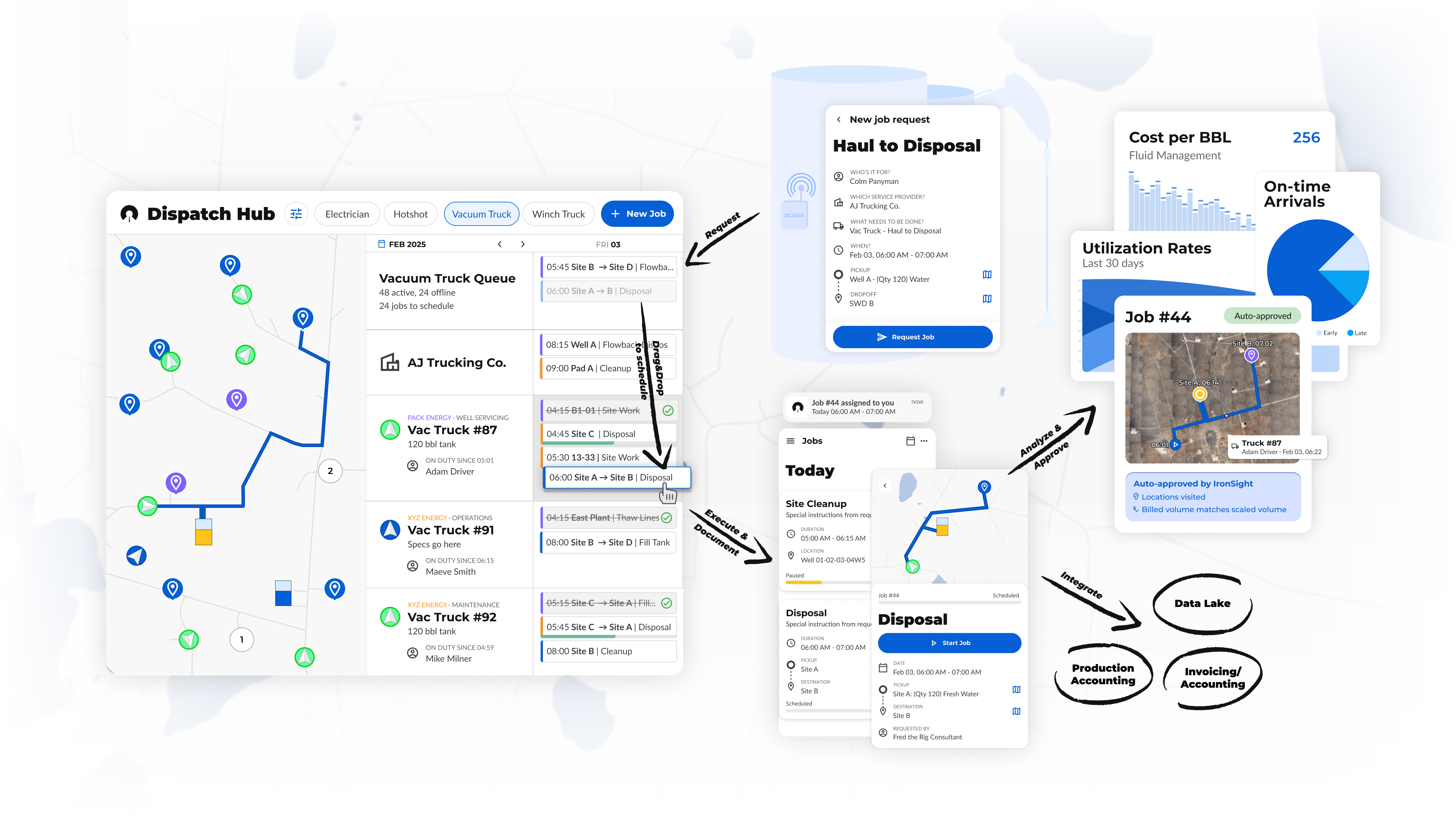
Trusted by leading operators and powered by advanced SCADA technologies
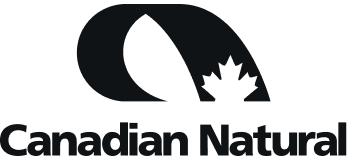
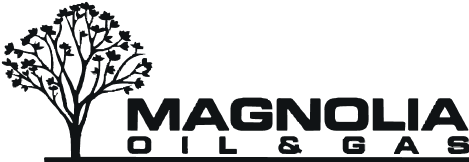

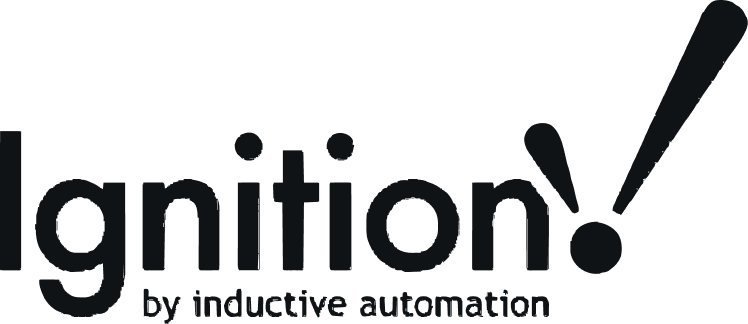
How are fluid volumes traditionally tracked?
Fluid haulers move production fluids from tanks on well pads to plants, disposal facilities, and sales terminals (or vice versa). They write-up paper trucking tickets that are the source of truth for fluid hauling data, and are the method by which trucking companies get paid (by the hour or by the volume hauled). Tickets need to be approved by the oil company with a stamp or signature. A copy is left at the pickup location, a copy is left at the destination, and a copy is kept by the driver as backup for invoice processes. The oil company collects thousands of these tickets every month and manually transfers the data into their production tracking software. Before IronSight became a technology company, we started out as an oilfield services provider called Pack Energy Services (see one of our tickets below).
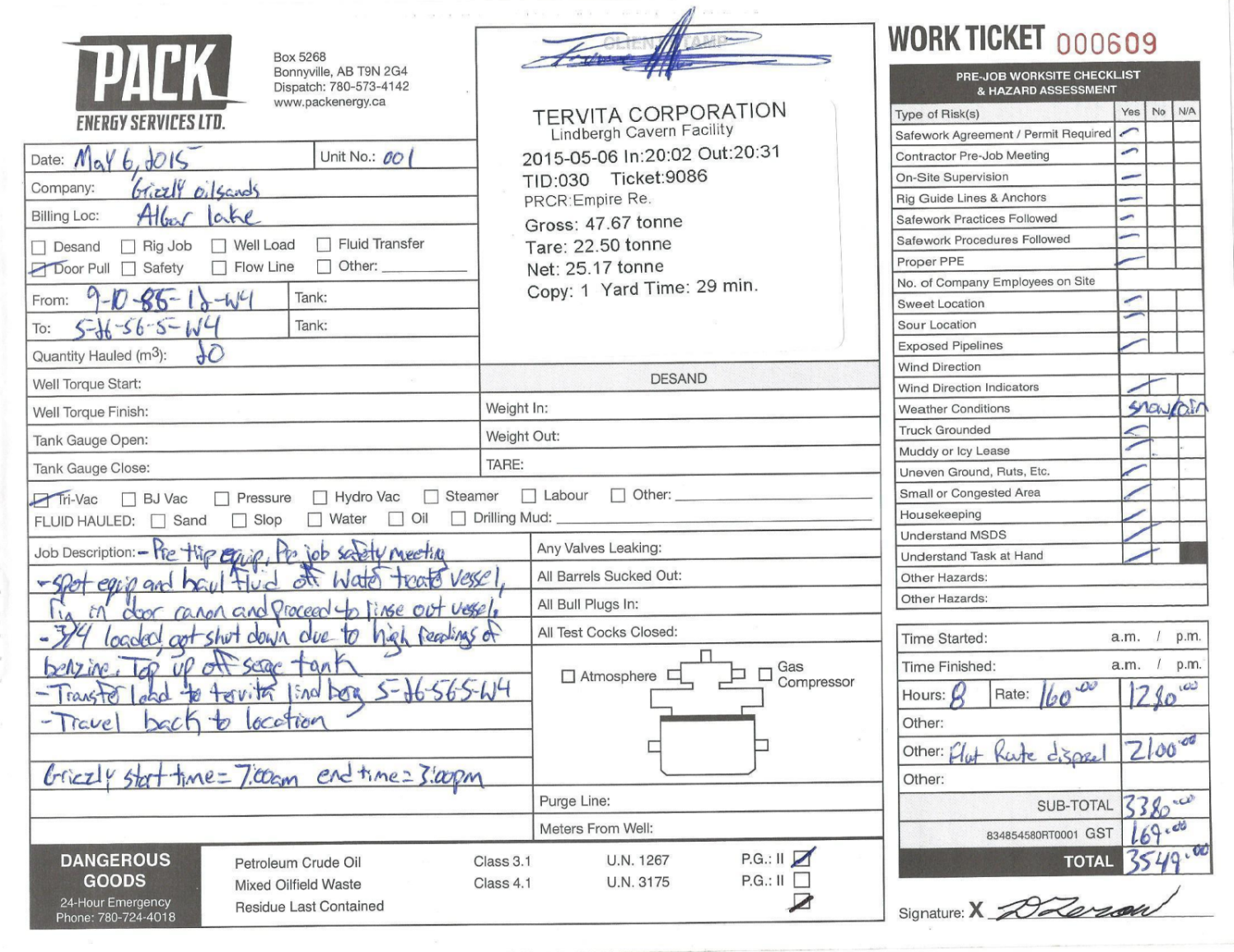
Challenges of paper-based truck ticketing
Paper-based ticketing systems create significant administrative strain for both energy producers (e.g., field operators and production accounting teams) and service providers (e.g., billing departments). Key pain points include:
Delayed data
Ticket information isn't available in real-time, leading to a lag between ticket creation and data entry into production systems.
Manual entry
Transferring data from paper tickets to digital platforms is labor-intensive and prone to errors.
Data quality
Discrepancies often occur between planned and actual haul volumes or destinations, compromising data integrity.
Reconciliation efforts
Manual matching of paper tickets with software records, disposal facility bills, or hauler invoices is time-consuming and complex.
Operational inefficiencies
Significant time is lost in the physical management of tickets, including writing, approval processes, and collection from various sites.
Extended billing cycles
The manual handling and processing of paper tickets can significantly prolong billing cycles, delaying revenue recognition and impacting cash flow.
Darcy Cretin
Superintendent
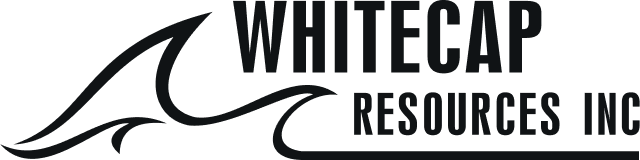
How fluid haul works in IronSight
SCADA or field operator requests job
Fluid haul jobs can be requested manually on our app or triggered automatically by SCADA tank sensors. An algorithm predicts when the tank will have a full load, and a jobs is created days in advance.
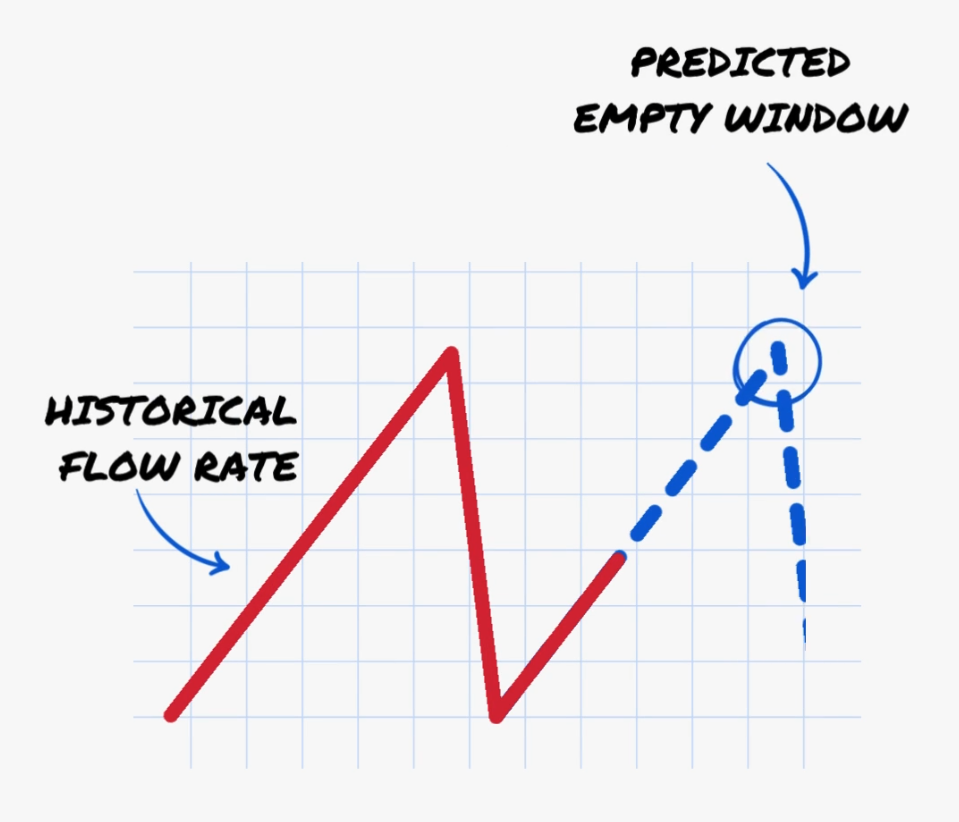
Coordinator or algorithm assigns job to service provider
Leveraging custom business rules, IronSight intelligently auto-assigns each job to the most suitable service provider. This algorithmic assignment optimizes resource utilization and adheres to predefined service criteria. Jobs can also be manually dragged-and-dropped to by internal coordinators.
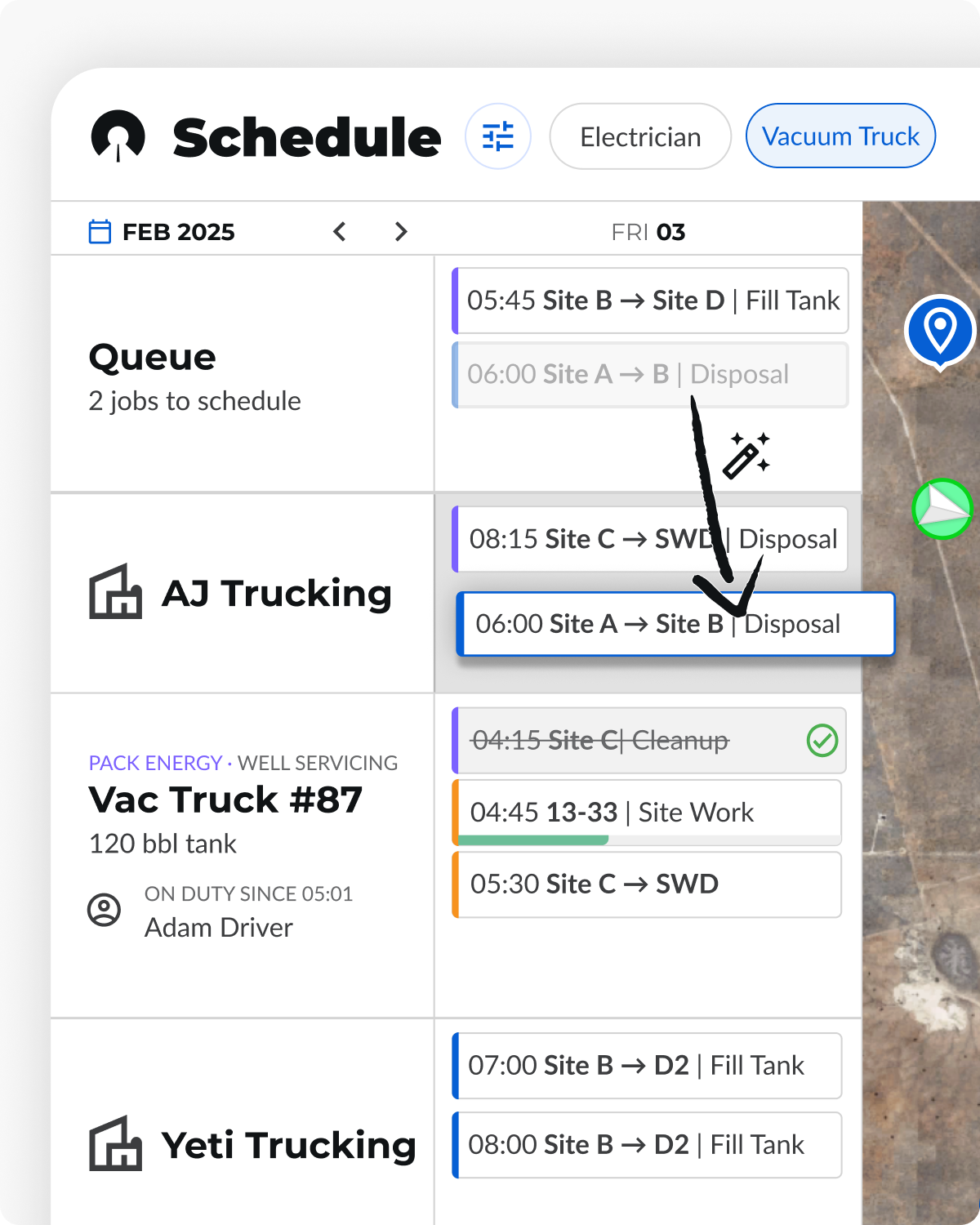
Service provider dispatches jobs to their truck & driver
The assigned service provider is notified and can log into IronSight to assign their truck and driver. They only see the jobs assigned to their compny. A real-time schedule and helps them make the optimal dispatch decision.
.png)
Driver executes the job
As drivers execute the haul, IronSight provides live tracking, offering full visibility into the job's progress. This transparency ensures all stakeholders are informed and the required volume, time, and mileage are tracked automatically for billing and reporting.
.png)
Driver or field sensors log inventory actuals
For facilities equipped with measuring devices, actual volumes are captured and linked to jobs via QR code scans. In locations without such equipment, IronSight's production accounting job forms come into play, prompting drivers to manually enter the volume and upload a photo of the scale ticket, maintaining accuracy and accountability across all unloading scenarios.
.png)
Service provider submits job for approval
Service provider billing admins can review comprehensive billing details, including job specifics, routes, time, and materials, in one centralized location. Once verified, jobs can be submitted for digital approval, streamlining the process.
.png)
Operator approves or rejects jobs
Manual approvals can be made confidently with a wealth of execution information, or an auto-approval algorithm can verify billed amounts against geofences, time-tracking, and volume tolerances, reducing ticket processing time by 80%.
.png)
Integrations sync data into other systems
Once jobs are approved, IronSight seamlessly exports the validated data to production accounting, invoicing, and accounts payable systems. This automated flow ensures accurate financial processing, eliminates manual data entry, and enhances overall operational efficiency by closing the loop from job request to financial reconciliation.
.png)
Ready to optimize
your fluid haul?
Schedule a call with our team where we can learn about your operations and provide a tailored demo.