Simplify Field Maintenance with IronSight
IronSight enhances your CMMS and/or ERP system by offering improved scheduling, execution, and documentation capabilities.
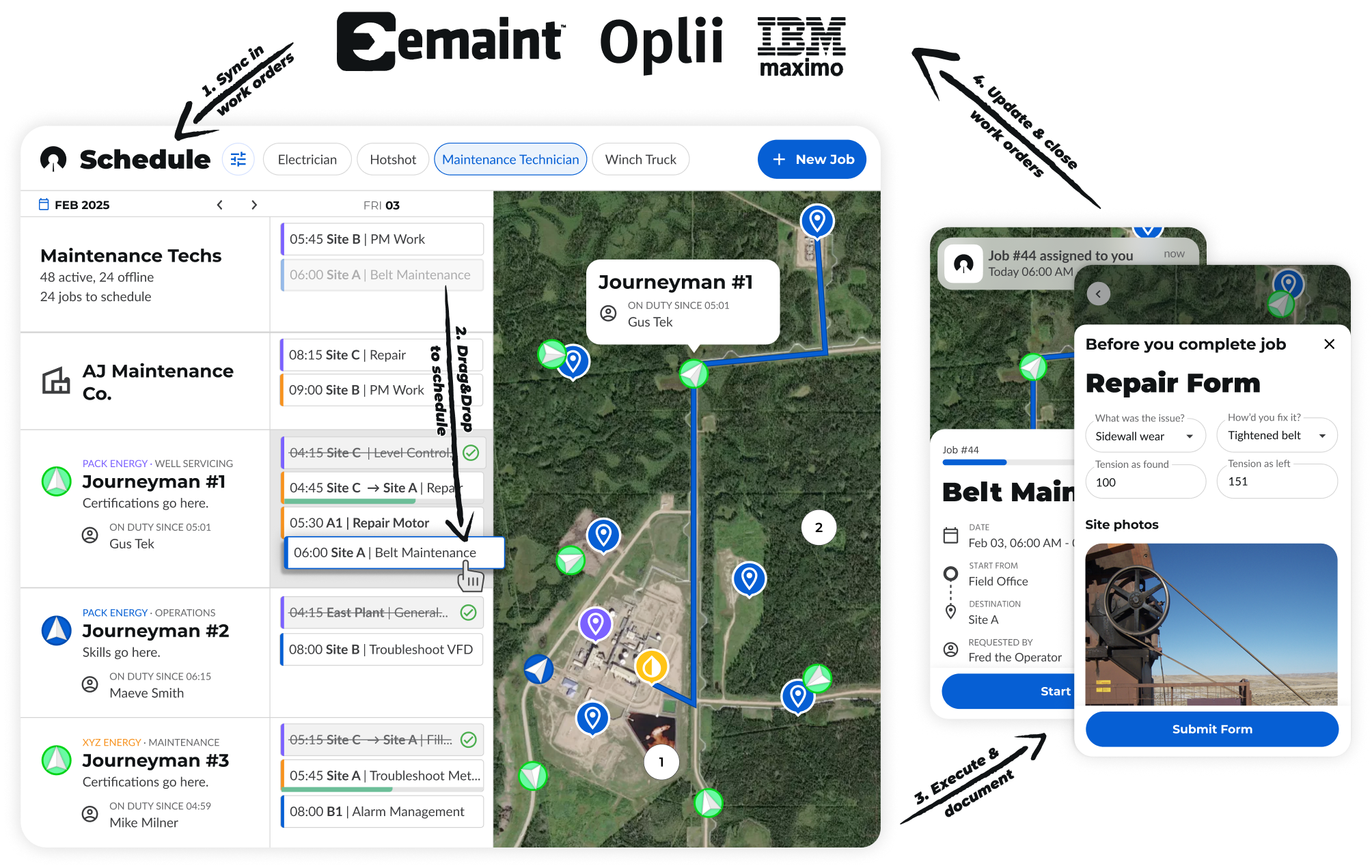
Trusted by industry leaders
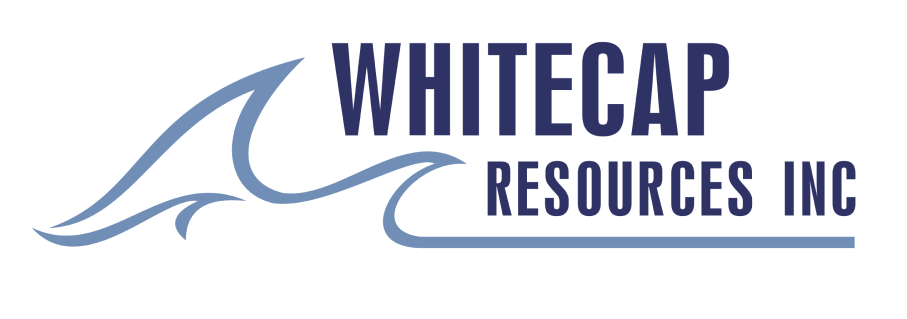
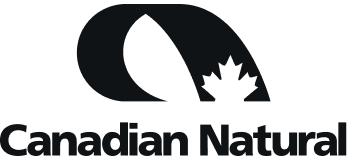
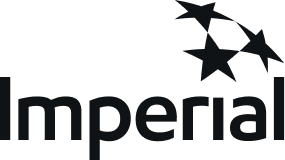
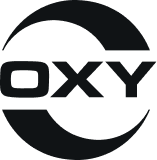
Your CMMS & ERP weren't made for the field.
IronSight is.
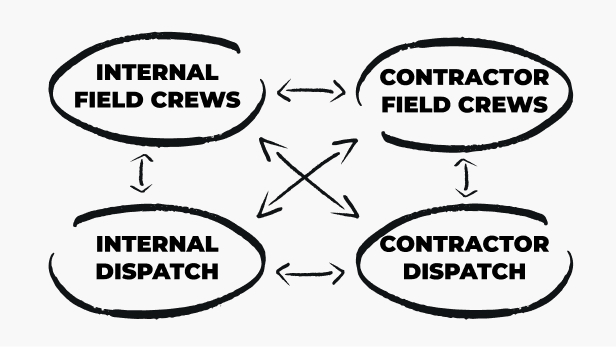
Collaborative
Whether your maintenance crews are employees, contractors, or a combination of both - IronSight just works.
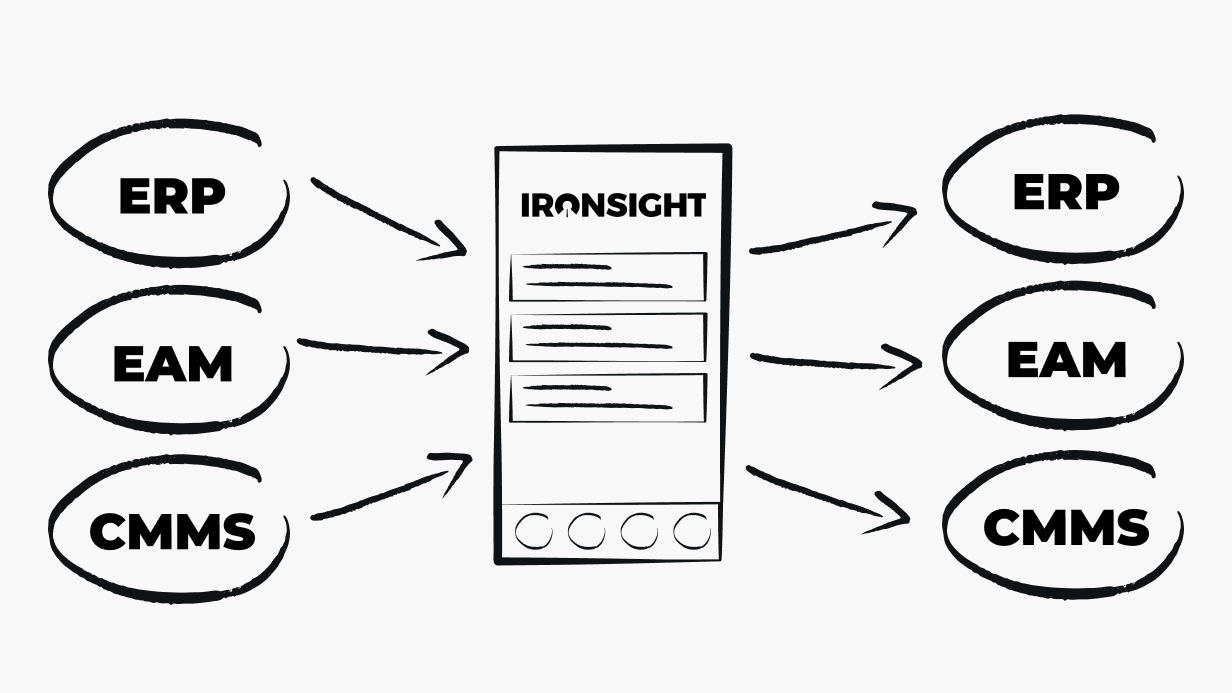
Connected
Connect your existing CMMS, ERP, EAM systems and more for a simple, connected, maintenance workflow.
View integrations
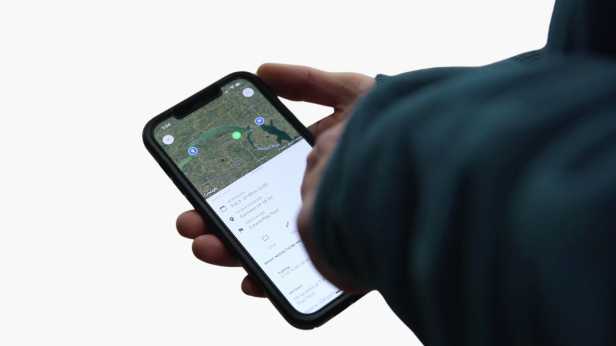
Made for the field
IronSight was founded in the field. Every design decision we make is focused on ensuring ease of use.
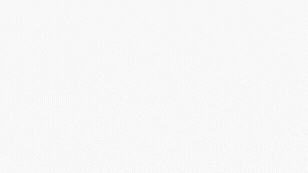
Versatile
Enhance all aspects of your operations by using IronSight for everything from fluid hauling to well servicing.
Speak with an expert
Schedule a call with our team to learn more about IronSight for maintenance.
How it works
Request correctives. Sync preventatives.
Preventive Maintenance (PM) tasks from your ERP/CMMS sync to IronSight for straightforward scheduling and execution. Completed PMs update and close through integration. Corrective Maintenance (CM) tasks are managed entirely within IronSight and then synced back, ensuring your ERP/CMMS has all the necessary data. This efficient workflow is designed for both internal technicians and contractors, improving your overall maintenance operations.
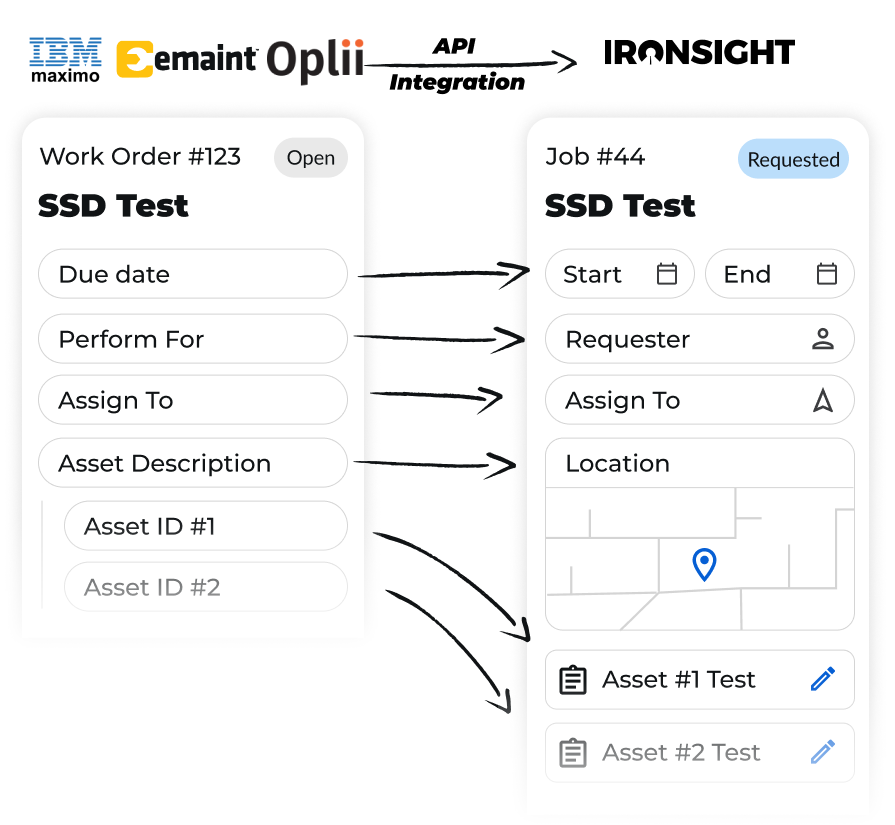
Schedule jobs to technicians
Elevate your maintenance coordination with IronSight, transforming it into a dynamic, real-time operation. Our platform empowers coordinators to schedule jobs to technicians from the office or on the go. Benefit from live updates and complete visibility to manage field operations with unmatched precision and efficiency.
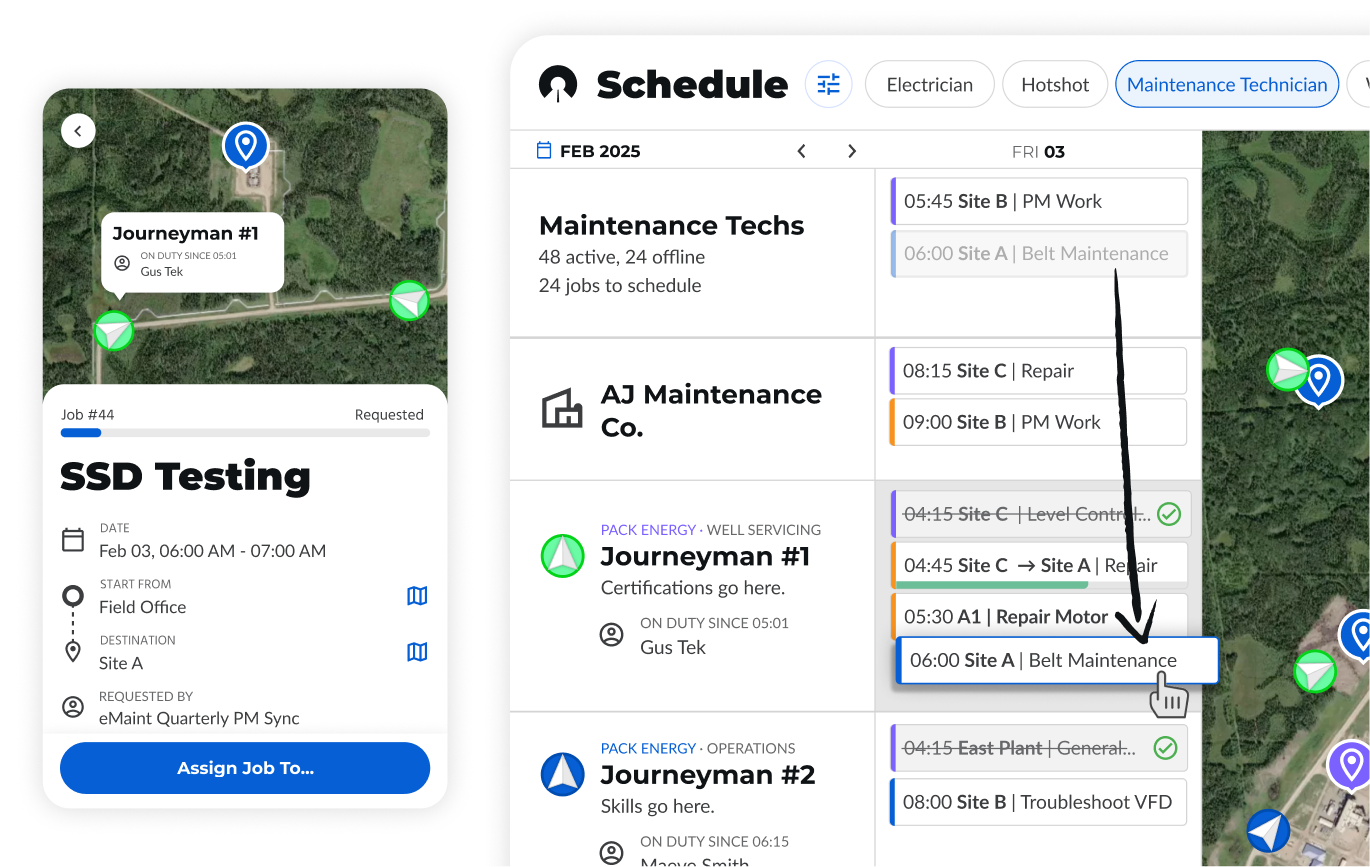
Empower your technicians
With IronSight, technicians receive comprehensive details for every job on IronSight's offline-capable mobile app: exact location, asset information, and specific action steps. This ensures they're fully prepared to execute their jobs with precision.
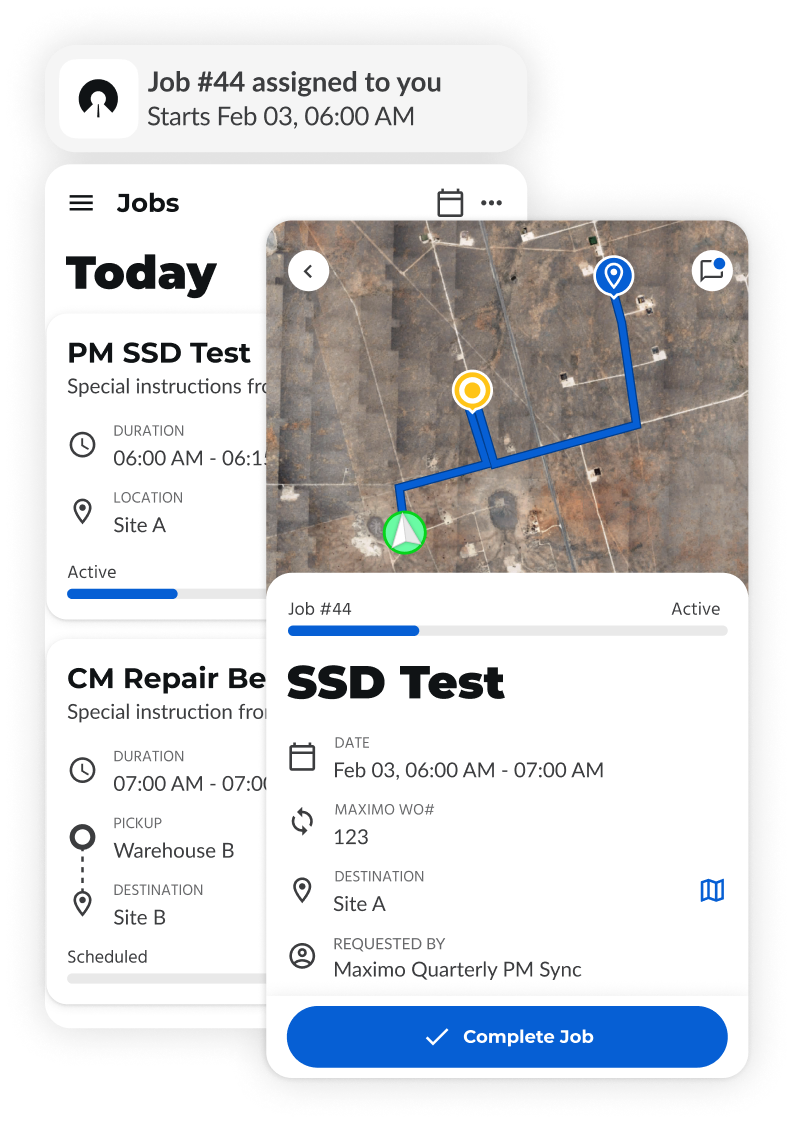
Capture on-site data
After completing a job, technicians can easily input detailed information about their work, including repairs made, maintenance performed, or inspection results, directly into IronSight. This step ensures all the crucial data is accurately recorded and available to sync back to your ERP/EAM/CMMS system.
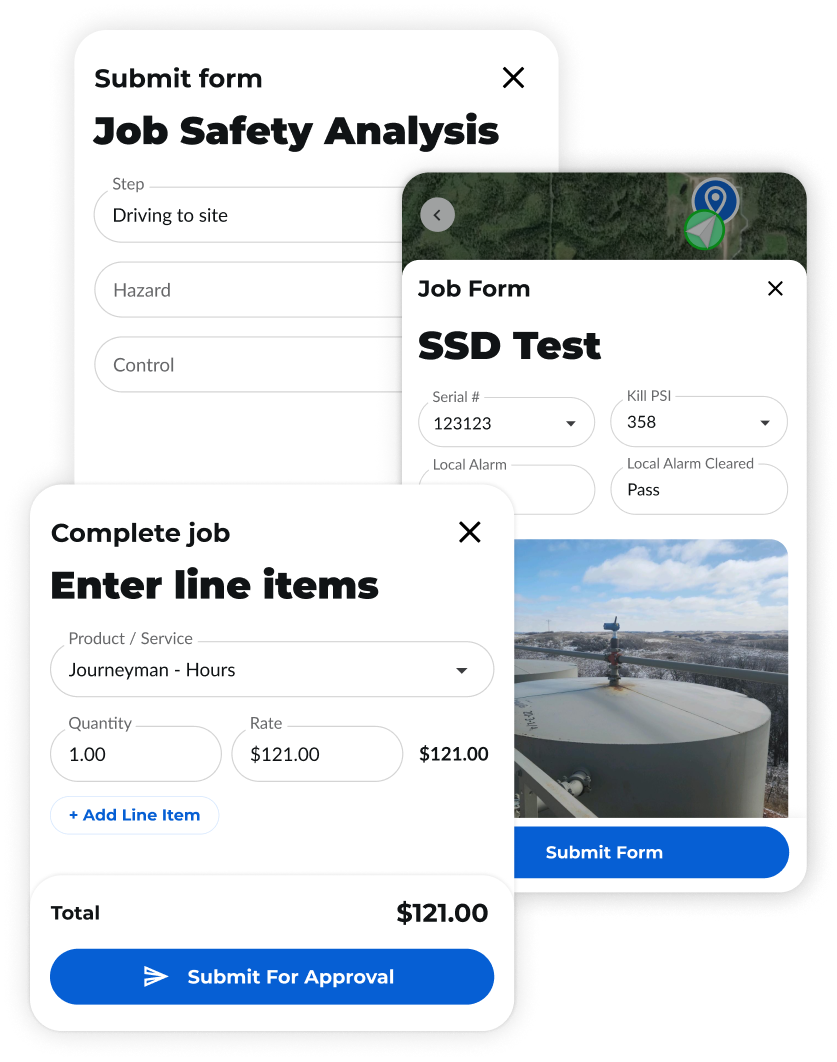
Maintenance insights
Technicians and coordinators can access IronSight's real-time dashboards for instant insights into maintenance activities. These dashboards provide an overview of job statuses, backlog, performance metrics, and trends, enabling informed decision-making and continuous improvement.
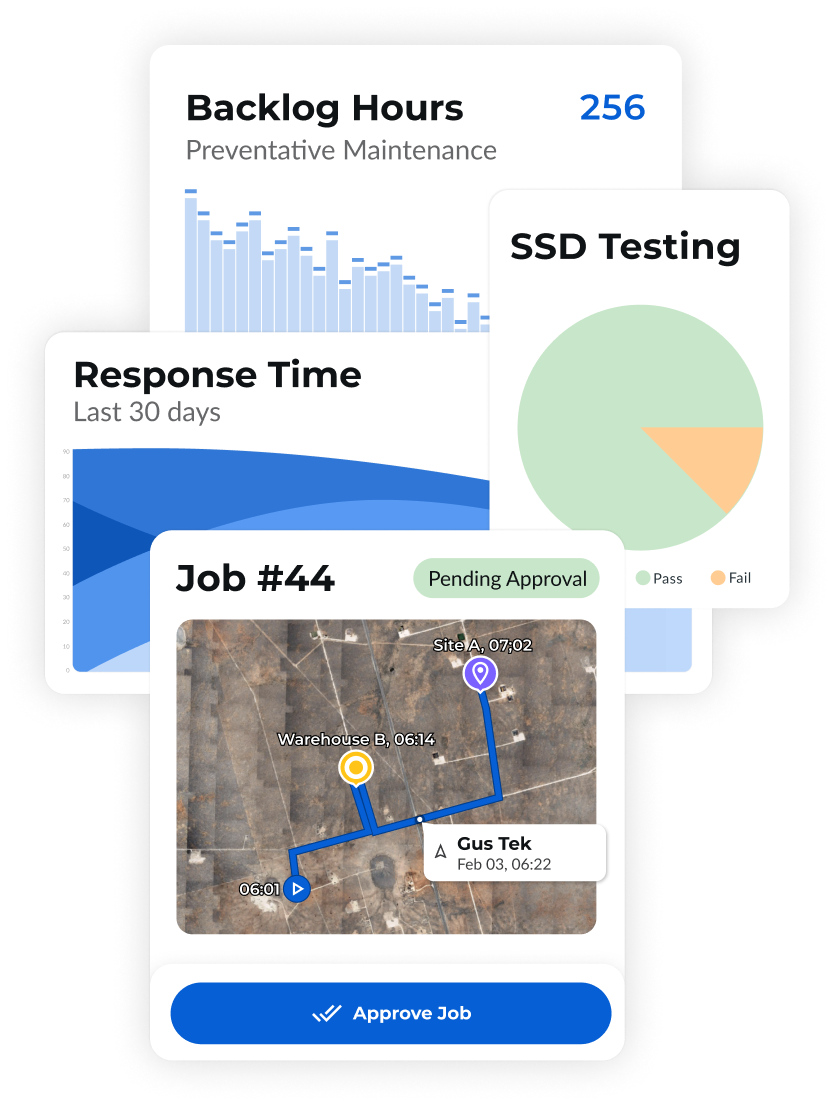
Automated work order closure and update
Upon job completion, IronSight automatically closes out the work order and updates the system with data captured by technicians. This seamless process ensures all records are accurate and up-to-date, streamlining post-job workflows and enhancing operational efficiency.
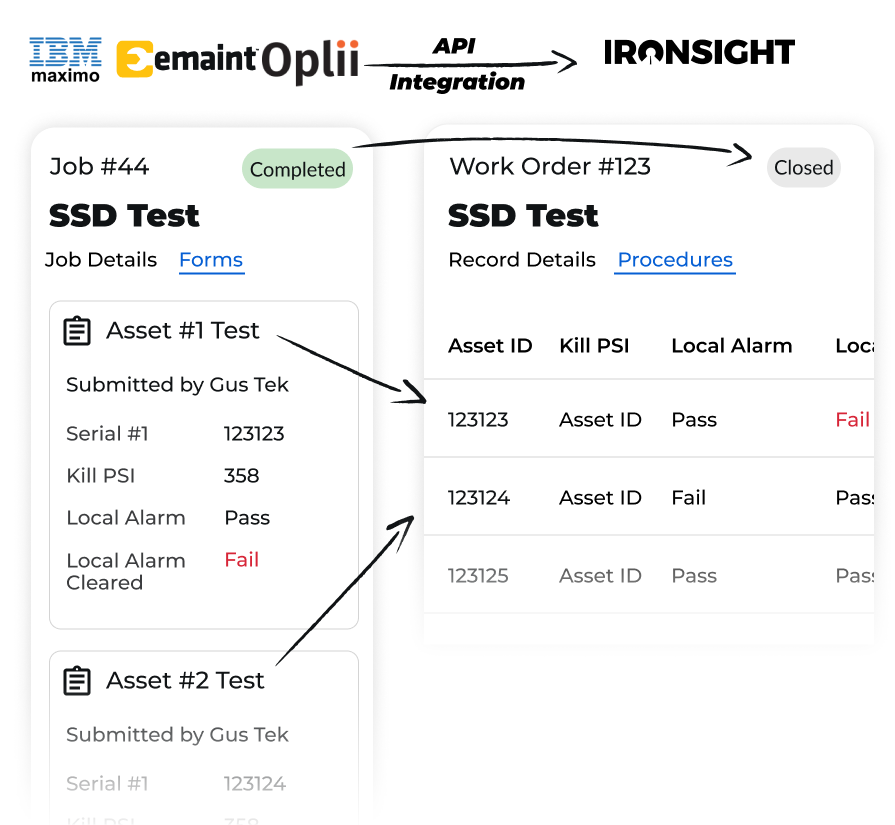
Ready to optimize
your field operations?
Schedule a call with our team where we can learn about your operations and provide a tailored demo.
Resources
Dive deeper into how IronSight can transform your operations with our targeted insights and integration guides.